In a lab in North Charleston, South Carolina, Roland Stone and Bart Stevens are helping set the stage for the future of sustainable aviation fuel (SAF).
To the untrained eye, it may look like these Boeing Research & Technology Materials, Process and Physics engineers are handling jars of water. But the testing vessels really contain jet reference fluids (JRFs) that mimic the broadest envelope of the chemistry and behavior of SAF.
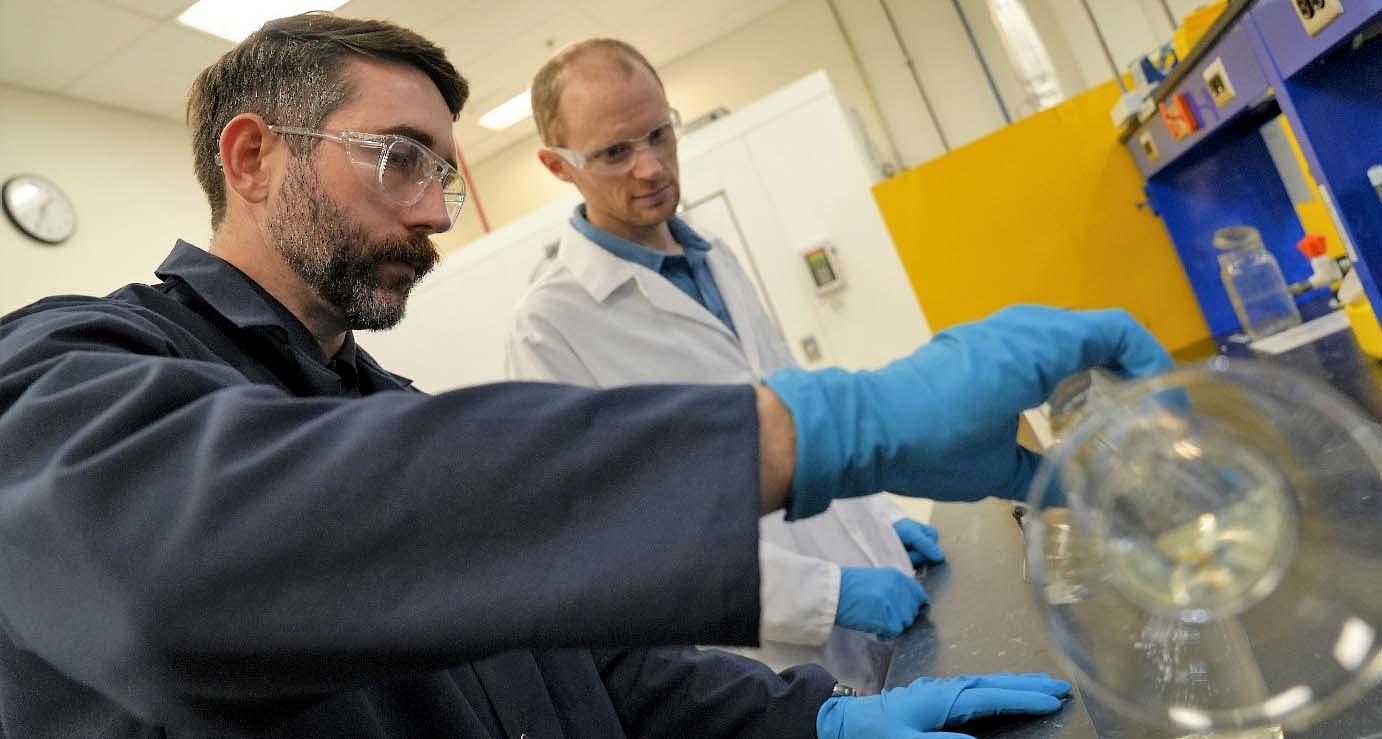
Roland Stone and Bart Stevens, two BR&T engineers who are a part of the Sustainable Aviation Fuel Compatibility Integrated Product Team, pour a sustainable aviation fuel jet reference fluid into a test vessel. (Kaitlin Stansell photo)
Samples of finishes, like paints and coatings used on current commercial airplanes soak in the JRFs with the goal to understand how SAF interacts with different parts of the airplane. The experts anticipate their research could also lead to findings that influence which paints or coatings are used in the future and test finishes that may appear on Boeing’s next generation of products.
Why it matters: “We are working to develop the next generation of materials, trying to get away from those that are hazardous to human health and the environment, like finding a non-chrome version of our fuel tank primer,” said Stone. “The data we are generating will provide that confidence of a new material that we would hopefully implement one day as an alternative.”
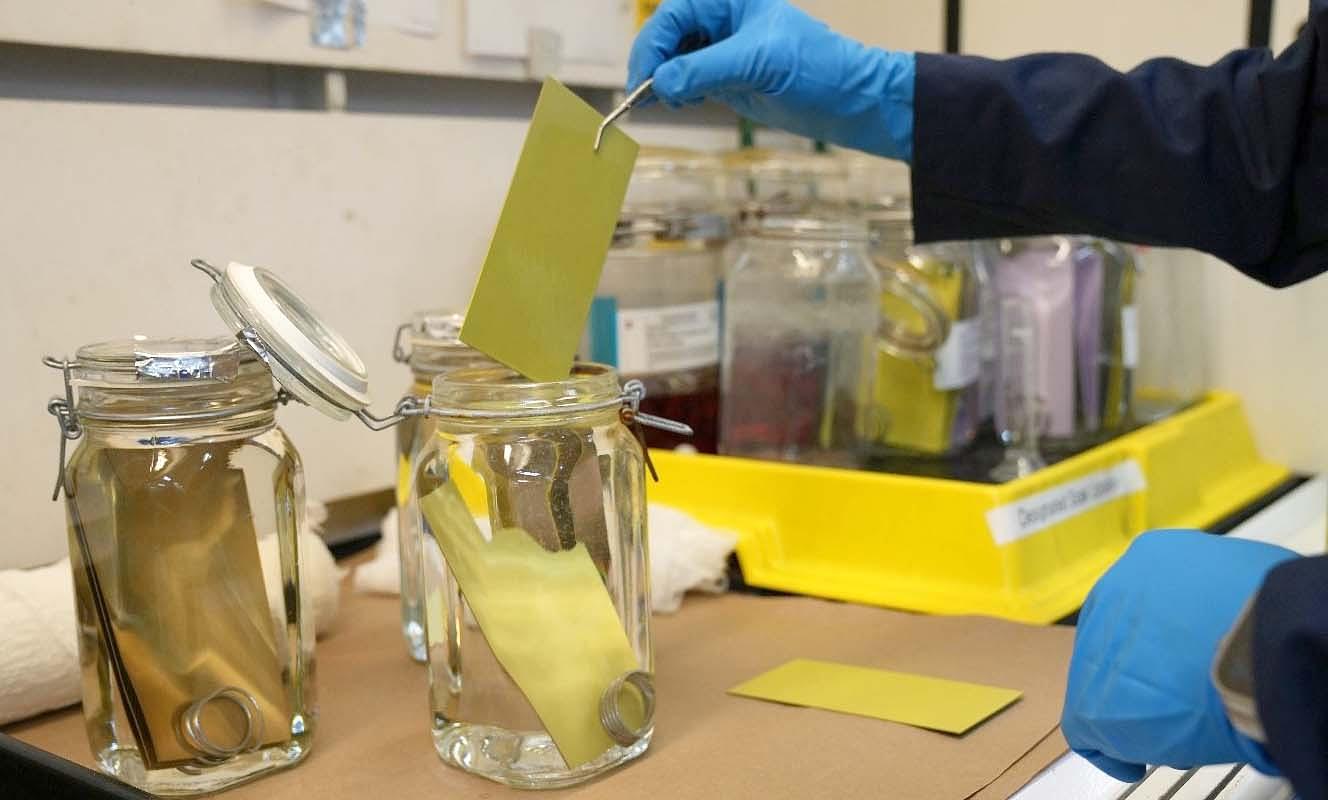
Roland Stone removes test panels from the SAF test fluids following an immersion in a hot water bath. (Kaitlin Stansell photo)
Testing their way to 100: Supporting the industry’s 2050 net zero emissions goal, SAF can reduce carbon emissions up to 80% over the fuel’s life cycle, and Boeing has committed all of its commercial airplanes will be compatible with 100% SAF by 2030.
Making sure its airplanes are 100% SAF compatible requires testing, and lots of it. Up for the challenge is a cross-functional SAF Compatibility Integrated Product Team (IPT) of 90-plus engineers anchored by the Sustainability and Technology team in Product Development.
Believing in the mission: For many involved in the project, the implications are personal.
“I am excited to go to work every day to contribute to this project.. The people I work with believe in the vision of a better world and are working together to make it happen,” said David Sims, an engineer leading several of the IPT’s materials groups.
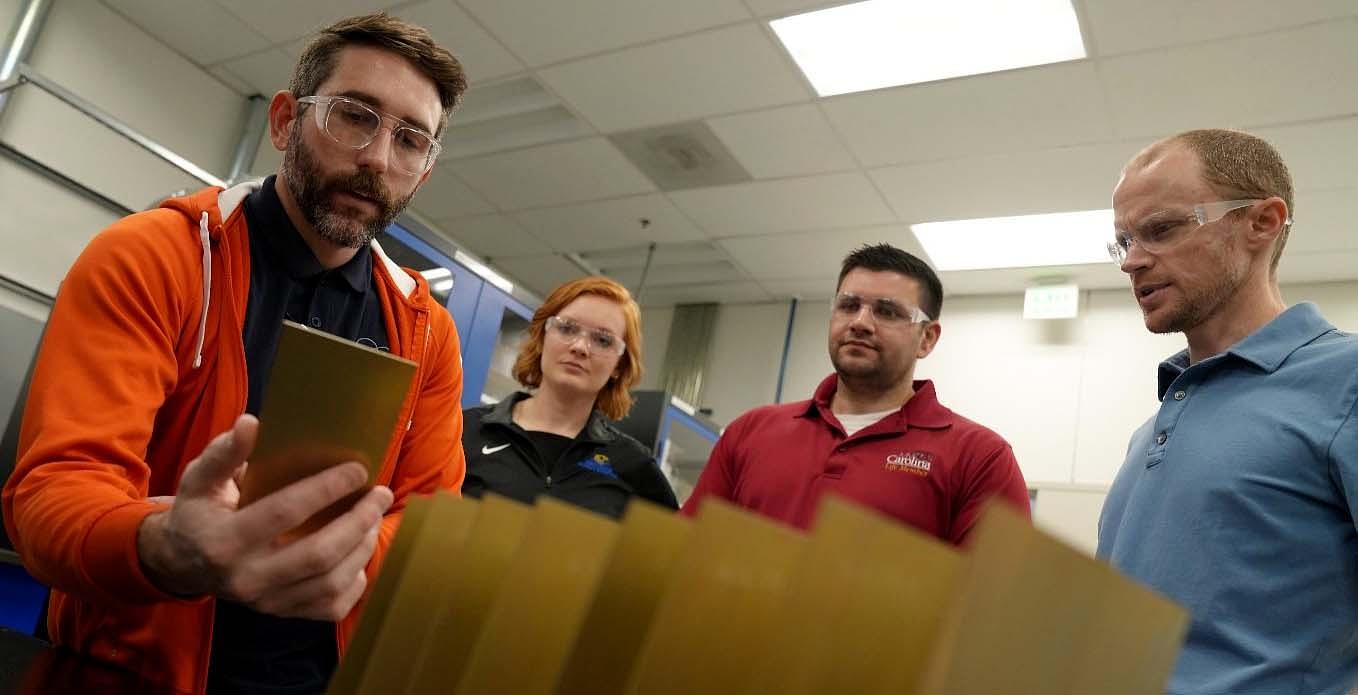
From left, Roland Stone, Jessica Savage, David Sims and Bart Stevens take a look at the test panels after they’ve cooled following time in an oven for exposure to high temperatures. (Kaitlin Stansell photo)
“I love traveling, and, at the same time, I see a world that needs to prioritize how we are using our resources,” said Jessica Savage, a materials integration engineer. “Not having aviation isn’t an option. But how do we do aviation the right way and build a world where you can fly, connect with other people, see other cultures and appreciate the things people do without harming the environment matters a great deal.”
Charting a flight path: Much of what the team is doing is novel, from test methods to the jet reference fluids they are using, with a range of fuel chemistries to simulate any SAF the industry could see in 2030 and beyond.
Additionally, the overall project is moving at considerable speed as the team collaborates with others around the globe, including Boeing’s suppliers, with a goal to complete testing of seven different material families by the end of 2024. That includes sealants, finishes, metals, elastomers, thermosets, thermoplastics and electrical wiring components.
“We want to move at pace with technical excellence, and that means we’re leveraging our global capabilities to hit our targets and generate these data packages to give us a better understanding of these materials,” Sims said. “The pace at which we are moving is exciting. Everyone is so bought in. It’s hard to believe what’s already been accomplished.”
Since February 2022, the team developed a roadmap to 2030 SAF compatibility, has built seven test plans, connected with Tier 1 suppliers and is actively coordinating with them to make sure their materials are compatible as well.
“The most incredible part is how we’ve all been working together. The working environment we’ve created is such a safe space for debate. The freedom to share your opinions is really valuable to the work we are doing,” Sims said.
By Kaitlin Stansell