For Emily Travis, collaboration is the key to innovation and the inspiration behind a new tool being used to assemble bin buckets at the Interiors Responsibility Center South Carolina (IRCSC).
The concept of the tool, known as the threshold trim installer, is simple, but it’s helped make the build process ergonomically safer while improving first-pass quality.
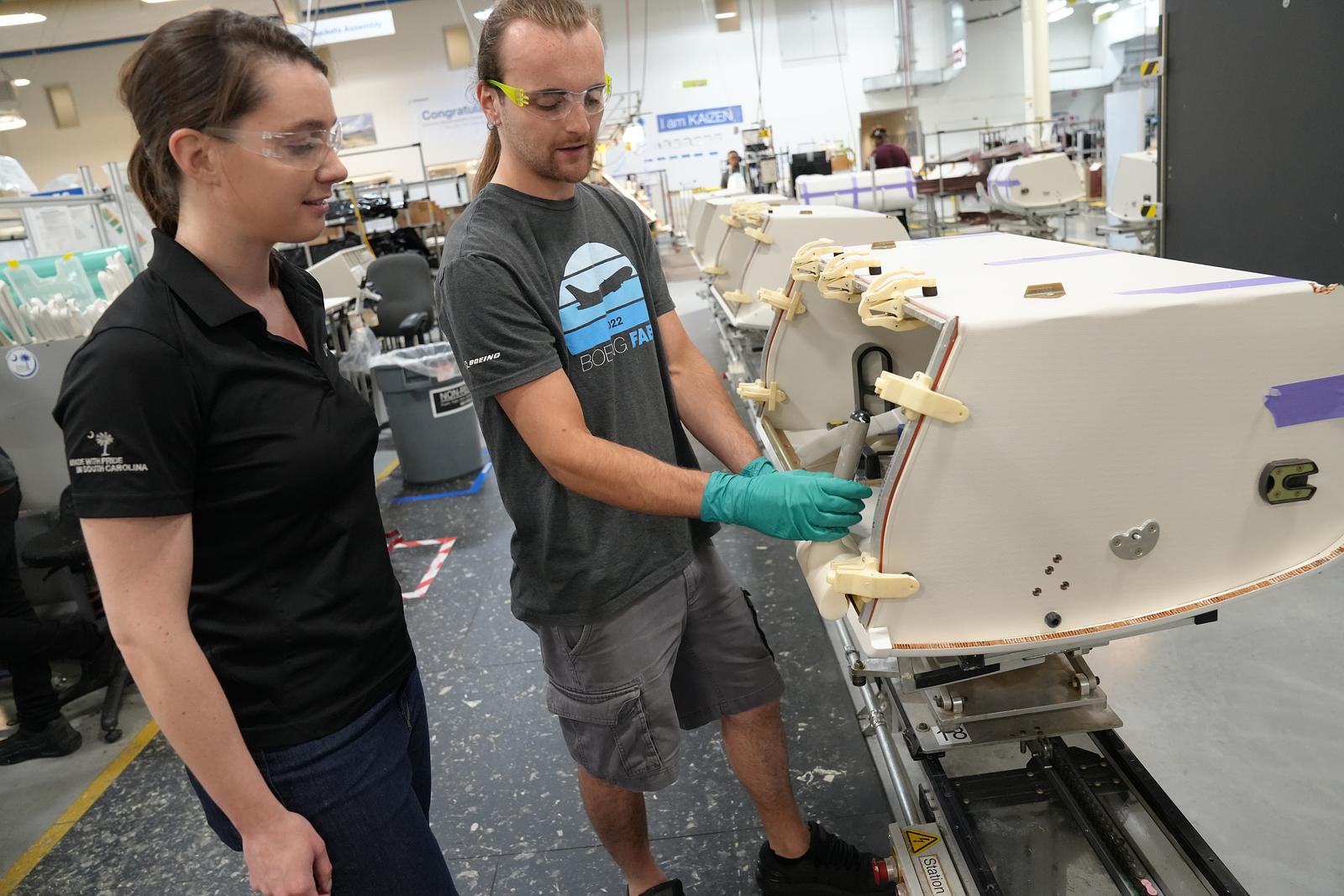
Emily Travis (left), a Tooling engineer at the IRCSC, collaborated with production teammates like James Brown to design a threshold trim installer that makes the bin bucket build process easier and ergonomically safer. (Kaitlin Stansell photo)
Before its use in the build process, teammates had shared their experiences with discomfort and fatigue as they pressed the trim into place by hand on every bin bucket.
“After assembling dozens of bin buckets each day, your thumbs would ache, and sometimes the trim would still have some waviness to it that you’d have to work out because it was difficult to get it flush with the part using your hands,” said Jeff Sheldon, the team lead for the bin bucket assembly at the IRCSC. “Now with the tool, the trim goes on right away; it’s ergonomically better and produces a higher quality finish every time.”
Travis recognized this as an opportunity to use her mechanical engineering background and 3D-printing expertise to make the build process ergonomically safer and easier.
“I devised a device concept that pivots to press the threshold trim into place using a handle to provide leverage,” Travis said. “I modeled and then 3D printed a prototype to try out the concept.”
But her first version of the tool didn’t go far enough.
“Although the general solution worked, the team wanted to be able to apply pressure across more of the threshold trim at once in order to save time,” Travis said. “After receiving their feedback, I made the device wider, and that’s the design they are using today.”
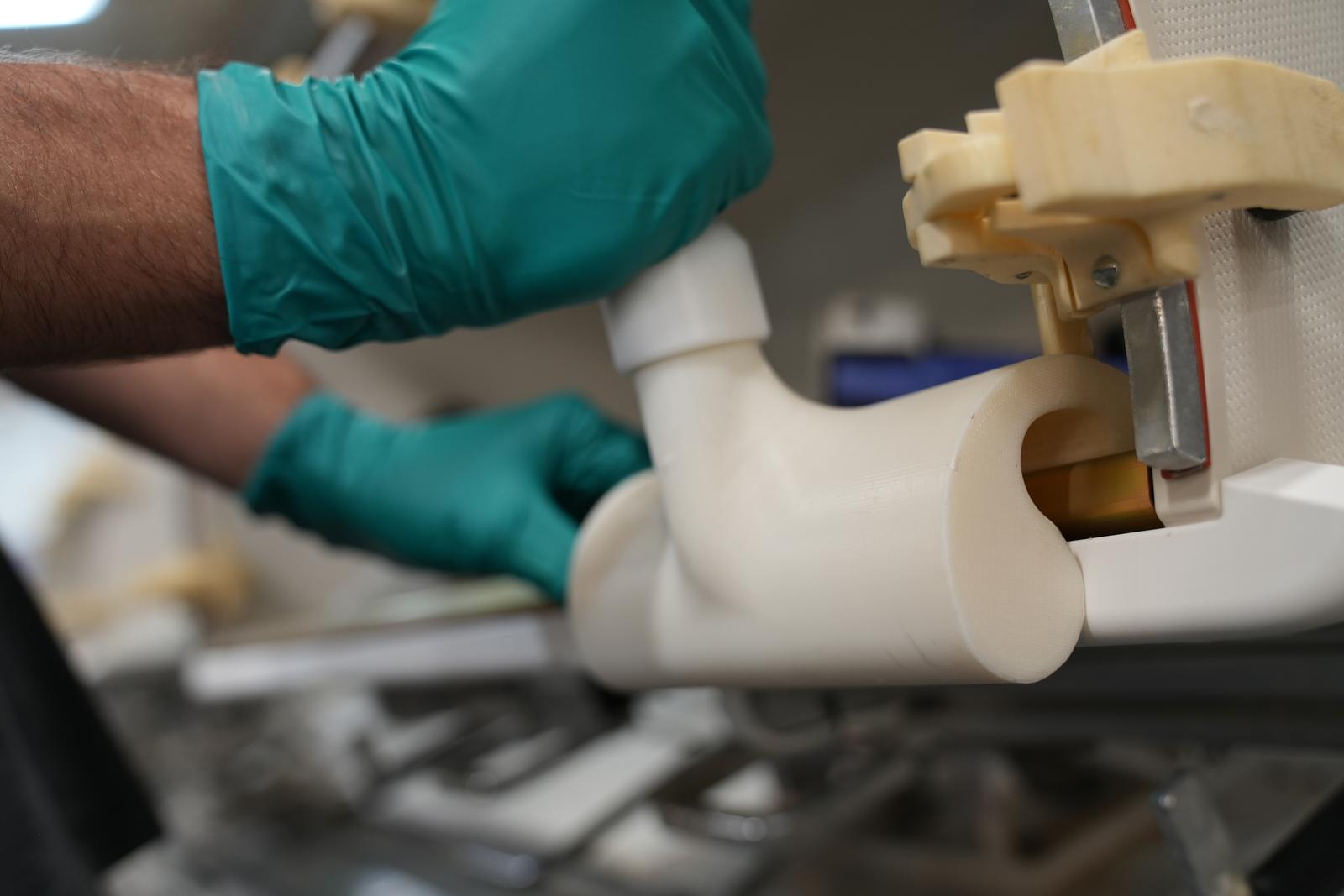
The threshold trim installer, inspired by production teammates at the IRCSC and designed by Travis, was 3D printed. (Kaitlin Stansell photo)
She says the collaboration between herself and the production team has been really rewarding.
“Coordinating with the team that will fabricate the solution as well as the people who will ultimately be using the final product is where collaboration really pays off,” Travis said. “Innovation doesn’t have to be complicated! In fact, the simpler the solution the better since that usually means the innovation will be more reliable and easier to use.”
Travis is just one of many teammates at Boeing South Carolina (BSC) contributing to a culture of innovation that is continuously improving products and the way they’re built.
Since 2009, more than 1,250 BSC teammates have received U.S. patent grants for nearly 800 unique inventions or processes. In 2022, BSC continued to lead the enterprise in invention disclosures per capita.
By Kaitlin Stansell